金屬激光切割機焦點控制系統的設計
2017-5-2 來源:武漢理工大學自動化學院 作者:朱云峰 聶紅偉
摘要:焦點控制系統是金屬激光切割機至關重要的組成部分,它與激光焦點與工件之間距離的準確性和穩定性直接相關,由此決定了金屬工件的切割質量和效率。 為此,采用高性能 DSP、高精度電容傳感器等設計金屬激光切割機焦點控制系統,對激光焦點與工件之間的距離進行實時精確的控制并配合機床運動控制卡完成整個金屬激光切割流程。 首先介紹了金屬激光切割機焦點控制系統的結構和工作原理,然后重點介紹了系統硬件設計,同時給出了部分核心軟件設計流程。
關鍵詞:金屬激光切割機,焦點控制系統,DSP,電容傳感器
在金屬激光切割過程中,激光焦點與工件距離的恒定極其重要, 采用焦點控制系統對其進行不斷的實時校正從而獲取最優的切割質量。采用高性能 DSP、高精度電容傳感器等設計金屬激光切割機焦點控制系統, 利用電容傳感器檢測技術和模糊 PID 控制算法對激光焦點與工件之間的距離進行實時精確的控制并配合機床運動控制卡協同完成整個金屬激光切割流程, 提高切割質量和切割效率。
1.系統結構和工作原理
1.1 系統結構
該系統主要包含兩個部分:焦點位置檢測模塊和焦點位置控制模塊。 焦點位置檢測模塊由電容信號檢測電路以及信號傳輸電路組成。 焦點位置控制模塊由電容信號的接收電路、電機控制信號的輸出電路、 指令信號的接收電路以及數據存儲電路組成,其功能是接收焦點位置檢測模塊發送的測量電容值,通過控制算法實時輸出電機控制信號,調控電機實現減小距離偏差的目的。
系統選用 TMS320F28335 型號的 DSP 作為主控制器,其時鐘頻率可達到 150MHz,I / O 資源豐富, 支持 SPI 通信、USB通信以及 DA 輸出等功能,能實現高效快速運算,從而實現與焦點位置檢測模塊以及機床運動控制卡的快速數據交換和運算。系統結構圖如圖 1 所示。
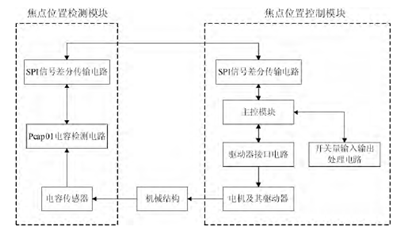
圖 1系統結構圖
1.2 工作原理
金屬激光切割機焦點控制系統的任務是對激光焦點與工件之間的距離進行實時采集以及控制, 使其始終處于最佳切割位置從而提高切割質量, 同時與機床運動控制卡進行數據交換協同完成整個金屬切割流程。 通過電容傳感器對激光焦點與工件之間距離進行采集, 并通過信號處理電路以數字量形式傳給主控制器 TMS320F28335; 主控制器對此距離信號進行數字濾波以及最小二乘法曲線擬合, 從而得到焦點距離與電容值之間的對應關系曲線; 主控制器通過模糊 PID 算法以焦點距離以及焦點距離變化率作為輸入, 輸出控制電壓給驅動器接口電路以驅動伺服電機運動使得激光焦點與工件之間距離始終處于最佳,由此提高切割質量以及效率; 機床運動卡主要實現 XY 平面上的運動軌跡規劃, 焦點控制系統則是實現 Z 方向上的切割距離恒定, 二者之間通過 I / O 口進行運動狀態的數交換協同完成整個金屬切割流程。
2.系統硬件設計
2.1 焦點位置檢測模塊設計
綜合考慮測量范圍、 測量精度以及成本等因素, 選用德國ACAM 公司的 Pcap01 專用電容檢測集成芯片來設計焦點位置檢測模塊,實時獲取焦點位置。 Pcap01 電容檢測芯片內置 DSP信號處理單元,具有高精度、高速度等優良特性,檢測頻率可高至 500k Hz,電容測量結果具有 24 位精度,且具有超高的溫度穩定性和超低溫漂。 焦點位置檢測模塊結構圖如圖 2 所示。

圖 2 焦點位置檢測模塊結構圖
在金屬激光切割過程中,Pcap01 電容檢測電路將焦點與工件之間的距離值轉換為數字量, 并通過 SPI 通信方式將其傳給主控制器進行數據處理。 需要注意的是,二者之間的信號線需為雙絞屏蔽線且在每組差分信號線之間要添加 1K 的匹配電阻,從而消除差分信號傳輸線的共模干擾, 在一定程度上加強遠距離信號傳輸的穩定性。
2.2 焦點位置控制模塊設計
焦點位置控制模塊由主控模塊、 驅動器接口電路以及開關量輸入輸出處理電路三部分組成。 主控模塊接收焦點位置檢測模塊發給的電容信號, 并根據電容值與焦點距離的標定關系得到此時的焦點距離, 并輸出通過模糊 PID 控制算法得到的對電機的控制電壓信號。 驅動器接口電路對 DSP 輸出的焦點位置控制模擬量電壓信號與電機驅動器輸入范圍進行匹配。 開關量輸入輸出處理電路的功能是接收機床運動控制卡發送的指令信號,并將焦點位置控制模塊的狀態反饋給機床運動控制卡,從而使焦點位置控制模塊處于正確的工作流程。 焦點位置控制模塊結構圖如圖 3 所示。
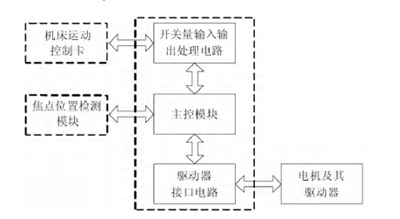
圖 3 焦點位置控制模塊結構圖
主控模塊由一個 DSP 最小系統、 外部存儲器以及外部 DA共同組成。 其功能為通過接口電路與機床運動控制卡進行 I / O 信號類型的數據交換、 接收焦點位置檢測模塊反饋的電容測量值、輸出對電機驅動器的控制電壓。 主控模塊硬件框圖如圖 4 所示。
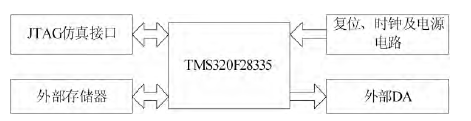
圖 4 主控模塊硬件框圖
本設計選取的 DSP 型號為 TMS320F28335,電壓輸出范圍為 0~3.3V,電機驅動器的控制電壓范圍為-10V~10V,驅動器接口電路采用運算放大器來實現匹配,其電路圖如圖 5 所示。

圖 5驅動器接口電路
對于金屬激光切割機而言, 機床運動控制卡實現的是 XY平面的切割軌跡規劃, 焦點控制系統實現的是 Z 方向的激光焦點位置的恒定,焦點控制系統要受機床運動控制卡的控制。 在金屬切割過程中,機床運動控制卡會發送隨動、穿孔、加工完成等信號給焦點控制系統, 而焦點控制系統也需要將反映當前切割頭位置的信號如上升到位信號、 下降到位信號以及切割報警信號等發送給機床運動控卡, 機床運動控制卡接收到這些信號后對其進行分析從而決定可否進行下一步的切割操作。 由于不同機床運動控制卡的開關量輸入輸出方式可能存在差異, 考慮到機床運動控制卡不同的電平電壓, 需要有一個相對適用范圍更廣的輸入輸出處理電路。 開關量輸入輸出處理電路原理圖如圖 6 所示,與機床運動控制卡通信信號全部進行光耦隔離,并通過指示燈進行示意。
3.系統軟件設計
3.1 主程序
主程序主要功能:系統初始化設置、焦點位置與電容值之間的數據標定以及回零操作。各個功能封裝成對應子程序,分別為初始化子程序、數據標定子程序和回零子程序,其流程圖如圖 7 所示。
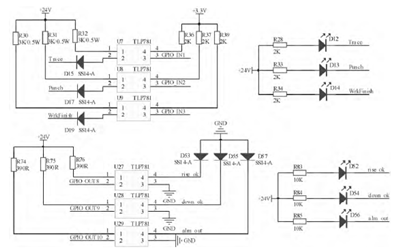
圖 6 開關量輸入輸出處理電路原理圖
數據標定子程序流程圖如圖 8 所示。 在數據標定子程序中,在每個已知距離的測量點處通過 Pcap01 電容檢測模塊測量電容并進行中值濾波, 將測量范圍合理分段后在每一小段上通過最小二乘法進行曲線擬合,實現焦點距離與電容值之間的標定。
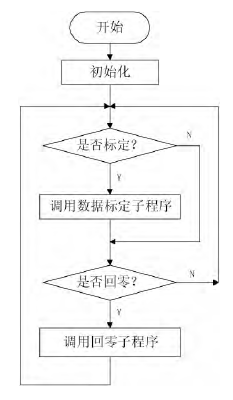
圖 7主程序流程圖

圖 8數據標定子程序流程圖
需要注意的是,當工件材質或者工作環境改變時,焦點距離-電容值特性曲線也會隨之而變化,此時必須重新進行數據標定。
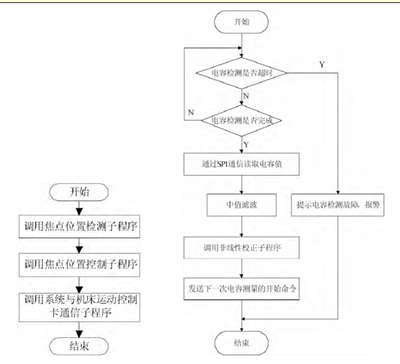
圖 92ms 定時中斷子程序流程圖 圖 10 焦點位置檢測子程序流程圖
主控制器中還有一個 2ms 定時中斷,其包含 3 個子程序:焦點位置檢測子程序,焦點位置控制子程序和系統與機床運動控制卡通信子程序。 焦點位置檢測子程序實現主控 DSP 對電容檢測單元的電容值讀??; 焦點位置控制子程序實現主控 DSP 對電機的控制電壓輸出;系統與機床運動控制卡通信子程序接收到的指令信號對應著系統不同的工作狀態,其決定著焦點位置檢測子程序中程序的走向。 2ms 定時中斷子程序流程圖如圖 9 所示。
3.2 焦點位置檢測子程序
焦點位置檢測子程序的功能是實現主控制器與電容檢測芯片之間的數據通信,獲取切割頭與工件之間的電容值,并通過由數據標定子程序確定的焦點距離與電容值擬合曲線解析式對應的焦點距離值,供焦點位置控制子程序調用。 焦點位置檢測子程序流程圖如圖 10 所示。
3.3 焦點位置控制子程序
焦點位置控制子程序的功能是讀取焦點位置檢測子程序接收的焦點距離反饋值, 并將反饋值代入模糊 PID 控制算法中從而獲取所需的對電機的控制電壓信號, 實現焦點距離的閉環控制。 焦點位置控制子程序流程圖如圖 11 所示。
4.實驗結果
在系統測試平臺上, 對系統的具體功能和性能指標進行詳的測試。 設置完激光切割參數后 (激光焦點位置參數設置為1mm),系統執行回零操作使切割頭位于高處 ,按下數據標定按鈕系統進行自動標定;標定完成后,系統接收到機床運動控制卡發送過來的跟隨信號后會自動進行焦點位置調節。為了便于系統控制效果的定量分析,通過主控 DSP 輸出一路與焦點位置值成正比的模擬電壓信號, 并采用運算放大器對信號進行適當放大后再接入示波器進行觀測。 在測試過程中,主要是觀測在階躍信號輸入下系統響應速度以及跟隨穩定性。經過實際切割和示波器波形觀測,系統的測量精度要很高,偏差低于 0.05mm,焦點距離控制的精度也達到了 0.1mm,并且在啟動 2 個交流伺服電機模擬電磁干擾的情況下系統仍然能夠正常穩定工作;焦點控制系統滿足設計預期,符合金屬激光切割機的切割要求。
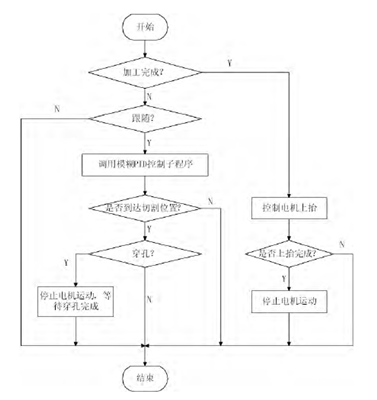
圖 11 焦點位置控制子程序流程圖
投稿箱:
如果您有機床行業、企業相關新聞稿件發表,或進行資訊合作,歡迎聯系本網編輯部, 郵箱:skjcsc@vip.sina.com
如果您有機床行業、企業相關新聞稿件發表,或進行資訊合作,歡迎聯系本網編輯部, 郵箱:skjcsc@vip.sina.com
更多相關信息