深孔加工振動斷屑裝置設計
2018-5-4 來源:中北大學;山西省深孔加工工程技術研究中心 作者:馬騰,沈興全,吳竹兵,胡寬輝
摘要: 針對深孔加工過程中切屑形態不穩定所形成的排屑不暢問題,基于振動鉆削理論,設計振動斷屑裝置,有效控制切削形態,保證順利排屑。通過給刀具施加軸向周期振動,振動斷屑裝置可實現變切厚鉆削和鉆頭軸向振動,使切屑易斷,并在一定程度上提高了表面加工質量。通過實驗探究了切屑形態與切削參數的關系,分析了振動斷屑裝置的最佳工作參數。
關鍵詞: 深孔加工; 振動鉆削; BTA 系統
1 、引言
深孔加工在封閉或半封閉的空間內進行,產生大量切屑在一定的空間內易形成堵塞,切削熱不易傳遞出去,其加工難度高、排屑難且工作量大。BTA 深孔鉆排屑的主要動力是由高壓油提供的壓力,如果切屑過長,即使在高壓油的作用下仍然難以排出。為解決深孔加工過程中排屑難的問題,通過分析振動切削原理、設計振動斷屑裝置、給刀具施加軸向周期振動,實現鉆頭瞬時切削厚度的改變和鉆頭軸向振動,從而有效控制切屑的形態,使切屑順利排出,提高高速深孔加工的效率。
2 、振動鉆削機理分析
振動鉆削的基本原理是通過振動裝置施加給刀具或工件一定方向、一定頻率和一定振幅的可控振動,使鉆頭和工件之間產生規律性的接觸和分離,從而使普通鉆削變成間歇式鉆削。針對不同的振動方向將振動鉆削分為三類(見圖1) ,其中,軸向振動方向與鉆頭的軸線方向一致,扭轉振動方向與鉆頭的旋轉方向一致,復合振動是軸向振動與扭轉振動的相互疊加。由于軸向振動比較容易實現且加工效果較好,因此應用最廣,其鉆削機理見圖2。
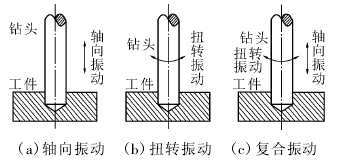
圖1 振動鉆削類別
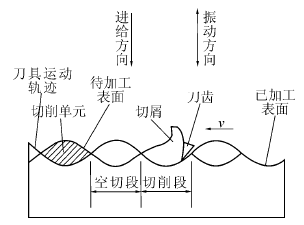
圖2 軸向振動鉆削機理
振動鉆削是間歇性切削,鉆削過程中鉆頭在極短的時間進行切削,其余時間鉆頭與工件都處于分離狀態; 鉆頭間歇式的切削使之獲得極大的瞬時速度和瞬時加速度,對被加工工件形成沖擊,使塑性金屬脆性化,同時降低摩擦系數和切削力,進而提高鉆頭的相對剛度。在振動鉆削過程中,由于鉆頭和工件間的接觸是間歇式的,因此振動鉆削產生的切削熱少且散熱快; 振動鉆削可以使切削力降低,并在一定程度上避免刀瘤的產生,提高加工工件的表面質量。
3、 振動裝置建模及分析
在設計機械式振動鉆削的振動裝置時,一般采用偏心機構、四連桿機構和曲柄滑塊機構等,綜合分析深孔加工的特點,擬采用偏心凸輪結構來建立模型。偏心式振動機構建模的基本原理見圖3。

圖3 偏心凸輪機構


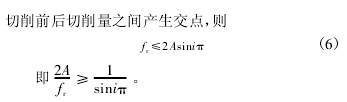
根據式( 6) 繪出如圖 4 所示的斷屑區域圖。

圖4 切削區域圖
4 、振動斷屑裝置設計
4. 1 振動發生裝置設計
振動鉆削裝置中必不可少的是振動發生器,其結構設計如圖 5 所示。由圖可知,內凸輪與轉軸采用緊配合的方式連接在一起,當轉軸轉動時,內凸輪隨之轉動; 為了實現振動振幅的調節,需要使內凸輪和外凸輪之間可以轉動,則外凸輪與內凸輪之間的配合方式為可動連接; 螺母可用來控制外凸輪與內凸輪之間何時可相對轉動,即當螺母松開時,外凸輪與內凸輪可以相互轉動。
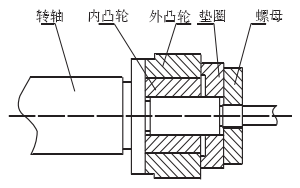
圖 5 振動發生器簡圖
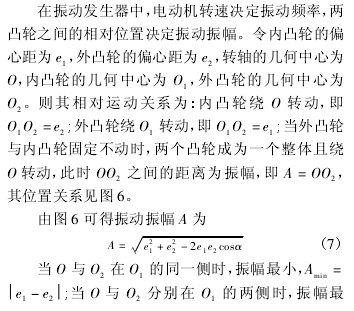

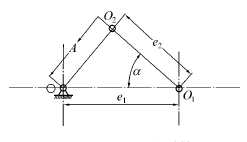
圖6 相對位置關系簡圖
4. 2 振動斷屑裝置整體設計
振動斷屑裝置整體結構見圖 7。由于鉆桿的不穩定性,振動發生裝置不容易固定,可將振動直接加載到聯結器上。為了使聯結器沿直線運動,設計安裝小導軌,其配合結構見圖 8。
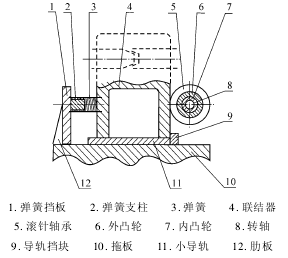
圖7 振動斷削裝置原理圖

圖8 小導軌與聯結器配合關系圖
為防止聯結器與小導軌脫離,設計安裝導軌擋于小導軌后端,可避免聯軸器掉落; 通過彈簧支柱把彈簧固定在彈簧擋板與聯結器之間,且彈簧處于壓縮狀態,其彈力足以推動聯結器移動。振動發生器的兩端支撐在拖板上,當凸輪轉動時,便會推動聯結器與鉆桿一起移動。振動斷屑裝置的特點包括: ①振動發生器可通過電機直接控制,則其振動頻率可通過調節電機的轉速實現控制; ②通過調節內外偏心輪的相對位置,可連續調節振幅大小,適應性強;③應用小導軌可保證鉆桿沿直線運動,從而保證了直線度; ④結構緊湊,易于安裝與操作,壽命長,性能穩定。
5 、振動斷屑裝置實驗分析
通過實驗探究振動參數與深孔加工中切削參數的關系。實驗設備包括: Z8Q16 臥式深孔鉆床、冷卻系統、振 動 裝 置、授 油 器、內 排 屑 深 孔 鉆 ( 8 ×500mm) 。實驗工件為 EA4T 車軸鋼,尺寸 30 ×300mm。實驗參數: 振動裝置振幅 A = 0. 08mm,機床轉速 n = 785r/min,油壓 3MPa。5. 1 斷屑實驗分析通過分析斷屑情況可知,振動鉆削產生的切屑與普通鉆削產生的切屑不同,普通鉆削所產生的切屑是厚度一致的帶狀切屑,而振動切屑所產生的切削的形態是隨振動頻率變化而變化。不同切削條件下振動斷屑的情況見表 1。

表 1 不同條件下切削斷屑情況

通過實驗分析不同振動參數下的切削形態,可得頻轉比 f/n 與切削形態關系如圖 9 所示。由圖可見,振動斷屑裝置有良好的斷屑效果,可以有效控制切屑形態。這種短小的切屑在高壓切削液作用下能夠順利排出,從而有效解決 BTA 深孔系統排屑難的問題。其特點為: ①形成瞬時切削厚度的改變有利于斷屑。當鉆頭振動切削時,由于鉆頭振動的作用,切屑受到隨振動變化而變化的切削力,表現出切屑厚度變化的特征。在高壓切削液的作用下,厚度不同的切屑在其薄弱處發生折斷,達到斷屑的目的。②形成鉆頭軸向的振動有利于斷屑。由于鉆頭在切削時進給量很小,所以軸向振動的振幅 2A 較易大于進給量,此時可實現分離切削,達到斷屑的目的。
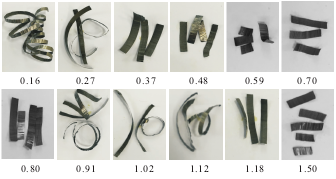
圖9 2A/fr= 5.5時,不同f/ n的切削形狀
5. 2 加工精度分析
通過實驗分析振動裝置對孔加工質量的影響。通過儀器檢測可得普通切削和振動切削時的成孔精度(見表2) 。
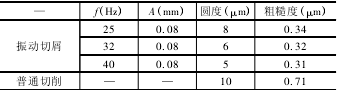
表 2 普通切削與振動切削成孔精度
通過對表 2 的分析可知,在其他加工參數相同時,振動切削能有效提高成孔質量,通過調節振動參數可以降低孔表面粗糙度,提高孔尺寸精度。分析其原因為:
(1) 在振動鉆削時,由于鉆頭切削扭矩變小,對成孔表面質量有積極作用。在振動切削的過程中,鉆頭在一瞬間內完成微量切削,使扭矩和切削強度相應降低,從而有利于改善表面加工質量。
(2) 在振動鉆削時,由于對切屑形態的控制使排屑更加流暢,對成孔表面質量有積極作用。振動切削可以使切屑變小,小的切屑在高壓切削液作用下順利排出,從而減小切屑對已加工表面的影響,避免打刀,提高刀具壽命。因此,振動切削可提高加工精度。
(3) 在振動鉆削時,可以對積屑瘤形成一定的抑制,所以對成孔表面質量有積極作用。普通切削會在切削區域內產生很大的擠壓力,在擠壓力作用下,隨著加工材料塑性變形會產生大量的切削熱,使切屑與刀具形成積屑瘤。積屑瘤對加工穩定性和刀具壽命都有不利影響,而且不利于保證成孔質量。振動切削過程中,由于鉆頭的振動使切削為間歇性切削,所以會使加工材料塑性化,使其塑性變形減小,減少積屑瘤的形成,達到抑制積屑瘤的目的。此外,由于振動切削的間歇性作用,切削時的潤滑和冷卻都會得到改善,積屑瘤的形成進一步得到抑制。
(4) 在振動鉆削時,由于切削液能更好地作用于切削,對孔表面質量有積極作用。在振動切削過程中,切削液在切削間隙能迅速進入切削區域,從而改善切削環境,接觸面之間的摩擦隨之降低,提高成孔表面的質量。
6、 結語
本文研究了振動鉆削原理,設計了振動斷屑裝置應用于深孔加工。振動斷屑裝置能有效地控制BTA 深孔鉆削加工時對切屑的控制,對深孔加工中切削形態控制和成孔質量具有積極作用。通過理論分析和實驗分析探討了振動鉆削斷屑裝置在深孔加工領域的可行性,為高速高效深孔加工技術的發展提供了一種可行性方案。
投稿箱:
如果您有機床行業、企業相關新聞稿件發表,或進行資訊合作,歡迎聯系本網編輯部, 郵箱:skjcsc@vip.sina.com
如果您有機床行業、企業相關新聞稿件發表,或進行資訊合作,歡迎聯系本網編輯部, 郵箱:skjcsc@vip.sina.com
更多相關信息