數控車床車削大直徑薄壁零件方法探析
2020-4-27 來源:- 作者:-
摘要:大直徑薄壁零件在車削加工中容易變形,難以保證零件的精度。著重從加工工藝的制定、工件輔助工裝的裝夾定位、車削程序指令的選用等方面進行優化設計,能有效減小薄壁零件的變形,提高薄壁零件的加工精度及質量。
關鍵詞:薄壁零件 數控車床 加工工藝
1、大直徑薄壁零件概述
某減速器上軸承襯套,是一種典型的大直徑薄壁零件。如圖 1 所示。
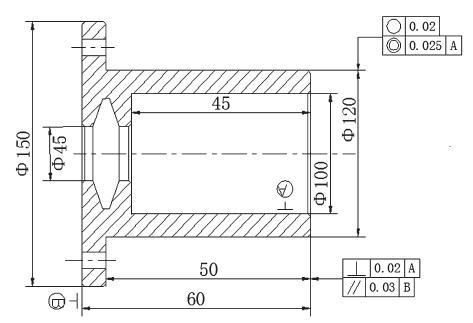
圖 1 大直徑薄壁零件
薄壁零件由于自身結構剛性差、強度弱,在車削加工中易產生振動及變形;夾緊力和切削力不均會造成零件形變;在車削零件中產生的熱能也容易使工件熱變形[1]。這些都是導致薄壁零件的加工精度不高的因素。在該零件生產制造過程中,通過工件定位與輔助夾具設計、制定合理可行的加工工藝、選用優良刀具和切削用量、優化刀具切削軌跡及程序等眾多措施,減少使薄壁零件在車削中易振動和變形的因素,有效提高零件的加工精度與加工效率。
2、零件工藝分析及制定
從零件圖紙技術要求及結構形狀來分析,此零件的加工難度是確保內、外圓的圓度與同軸度、各端面與軸線的垂直度等達到技術要求。零件毛坯料為 45 號鋼,Ф210mm×150mm 的實心棒材。削工藝安排粗加工、半精加工、精加工多道工序,使用普通車床進行粗加工和半精加工[2],通過增加半精加工這一道工序,能夠有效減小粗加工切削力和夾緊力較大、切削溫度較高所引起的工件變形及內應力。精車使用廣數 G210 數控車床切削加工,應用自制臺階軟爪安裝工件,精車內、外徑及端面,而后使用軟爪撐內孔安裝方式定位零件,完成后續工步制成成品。通過上述精車加工,滿足了先內后外與在一次裝夾內完成切削任務的工藝原則[3],有效減少零件因重復裝夾與定位所產生的工藝基準與定位基準的偏差。
3、工件定位與裝夾設計
廣數 G210 數控車床采用液壓卡盤裝夾工件,因液壓卡盤的卡爪夾緊力大、接觸面小,容易使零件產生變形。筆者設計了一個扇形臺階式軟爪,如圖 2 所示,精車工件之前,把軟爪安裝到卡盤上,采用“自干自”精密車削軟爪之后,軟爪精度值大幅度提高,軟爪夾持零件最大外徑處,就可完成在一次裝夾中車削零件內、外直徑與端面的工序,這樣確保工件裝夾定位精度。軟爪形狀制作成扇形是為了增大與工件的接觸面,可使軟爪夾緊力均勻分布在工件外表面,能夠有效降低零件受三點應力集中產生的形變[4]。
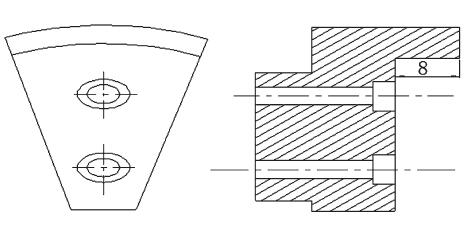
圖 2 扇形階臺軟爪
4、刀具和切削用量的優化
刀具優良的幾何角度可以提高加工精度,合理選擇切削用量有利于提高加工效率。刀具主要選用機夾車刀,如表 1 所示,選用 95°外徑車刀,因刀具前角、主偏角較大,切削性能好,不易使工件產生振動與變形。內孔刀具選擇刀尖圓角半徑為 0.2mm,使刀尖圓弧及修光刃長度減小,這樣可降低軸向切削力,不易使工件產生軸向跳動。車削內孔為防止積屑造成刀具加屑而形成的刀具讓刀現象,可選擇斷屑性能好的涂層刀片[5]進行加工。車削中還可通過加注乳化油類冷卻液對零件進行降溫,進而減少零件因熱能產生的形變。
表 1 刀具參數

為降低零件加工中的切削力,精車薄壁零件時切削用量不宜選用過大,減少因刀具剛性不足而產生的讓刀的現象[6],從而提高工件內表面加工精度值。
精加工零件時,削用量應選用較低的主軸轉速在 240 ~ 450r/min,背吃刀量在 0.1 ~ 0.2mm,進給量在 0.05 ~ 0.2mm/r,這樣的切削用量值,車削出的零件變形小、精度值高。
5、刀具車削軌跡與程序的選用
規劃走刀路徑及合理選用程序指令,可以有效減小切削零件中的切削力。工件裝夾在卡盤上后,會形成懸伸結構狀態[7],在加工零件端面時,若選擇從小徑向大徑方向的走刀路線,會增大車工件上的徑向力,進而引發車削端面時的振顫,使薄壁零件在端面及結合部產生變形[8]。若采用走刀路線從法向進刀來車削端面,并應用恒線速度功能指令——G96 S,可大幅度降低車削端面時的切削力,從而確保端面與外徑的形位精度及粗糙度值。
6、結語
憑借數控車床的高精度和高效率性能,通過制定合理的數控加工工藝,應用簡單可靠的輔助夾具,選擇適合的機夾刀具,就可有效減少薄壁零件在車削過程中產生的變形,從而有效地提高了零件加工精度與質量。
投稿箱:
如果您有機床行業、企業相關新聞稿件發表,或進行資訊合作,歡迎聯系本網編輯部, 郵箱:skjcsc@vip.sina.com
如果您有機床行業、企業相關新聞稿件發表,或進行資訊合作,歡迎聯系本網編輯部, 郵箱:skjcsc@vip.sina.com
更多相關信息