一種彎頭管嘴類零件車削加工的工藝優化
2020-12-3 來源:航空工業慶安集團有限公司 作者: 李 濤
摘要: 介紹了某航空產品120°彎頭管嘴零件的加工工藝及工裝設計方案優化過程,重點論述了工藝流程中如何選擇定位基準及夾緊方式,如何通過正確的基準轉換來確保零件加工質量,提高加工效率,進而形成規范的工藝流程及典型工裝設計。
關鍵詞:彎頭管嘴;定位夾緊;車削加工;快換系統
長期以來,無工藝附加彎頭管嘴類零件的加工過程中,始終存在零件定位不可靠、夾持不緊、跳動量超差的問題。本文涉及的某管嘴零件如圖 1 所示,依次加工兩油孔相貫錯位量大,形位公差超差嚴重,零件加工質量差,效率低,嚴重影響產品生產進度。

圖1 零件圖樣
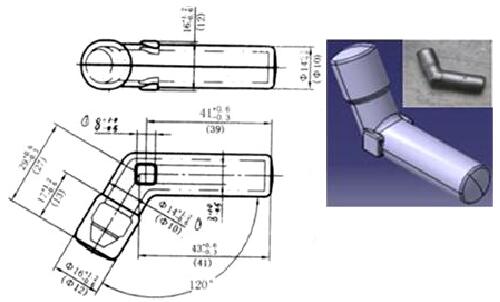
圖2 鍛件毛坯
1、 工藝分析
零件鍛件毛坯見圖 2 所示,鍛件表面錯移,表面不 規則,且無工藝附加,彎頭呈 120°夾角,頸部尺寸短,夾具難以設計可靠的定位、夾緊結構。現場采用自制夾具加工,經常出現零件尺寸超差,質量不穩定,效率低等現象,嚴重影響了零件的正常交付。圖 3 為原工藝流程。
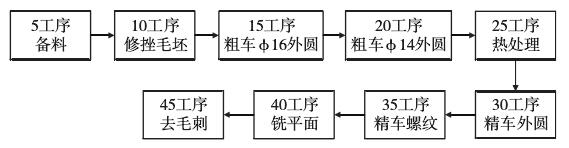
圖3 原工藝流程
1.1 原工序分析
15、20 工序,使用自制夾具見圖 4。工序基準為零件兩個外圓和其中心線交點,工件在夾具上的定位基準選擇與工序基準相同,符合基準重合原則的要求,但零件毛坯為鍛件且缺陷較重,零件兩次裝夾,定位基準選擇與工序基準均無法保證重合,定位夾緊不可靠,加上自制夾具沒有經過熱處理,使用時間長產生變形,導致粗車的兩端有偏移,不能保證零件兩端軸線在同一基準面上,120°夾角誤差較大,實際加工的工件表面形位誤差不能滿足后續加工要求。
30、35 工序,使用自制兩爪卡盤裝夾見圖 5,夾緊比較牢靠,但此夾具兩道精車工序分別使用 15、20 工序的兩個粗基準進行定位夾緊,理論上粗基準只能選用一次,而且自制卡盤兩爪材料未熱處理,長期使用后接觸面產生變形,夾具中心偏移,導致車削時外圓跳動量大,螺紋表面車削不出來,且難以保證零件兩端軸線在同一基準面上,120°夾角誤差也較大。導致零件兩中心油孔交叉錯位,造成成批量報廢、嚴重影響產品交付。
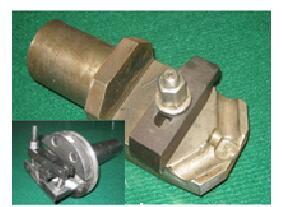
圖4 自制車外圓夾具
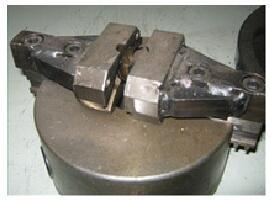
圖5 自制兩爪卡盤夾具
分析工藝方案,找出造成零件加工超差,不穩定的三點原因,見表 1,并有針對的提出改進措施,保證零件順利加工。
1.2 優化后的工藝流程
優化后的工藝流程如圖 6 所示,保證零件順利加工完成。
表1 方案優化措施表
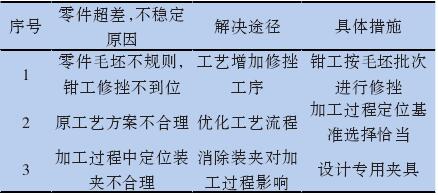
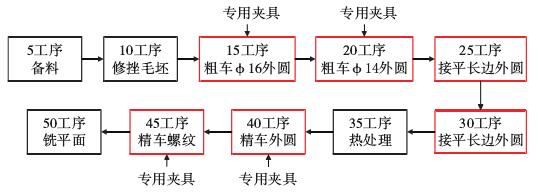
圖6 優化后工藝流程
2 、工藝及工裝優化過程
通常情況下,在機床上加工工件時,為保證加工精度,首先需要保證工件在夾具上正確定位、夾緊,使工件在機床上占有正確的位置[1],才能加工出合格的零件。為此梳理優化工藝流程,改變原加工策略,最終形成工藝及配套工裝如下。
2.1 粗車 Φ16 外圓
15 工序,粗車 Φ16 外圓至 Φ14。夾具設計如圖 7所示,采用了過定位原理,用雙 V 型同時定位,雙面夾緊的結構,其中一個活動 V 型塊可以調節夾具中心高,彌補鍛件毛胚來源不規則帶來的中心偏移問題,且材料選為耐磨性好的 Cr WMn,方便磨損后更換。另一固定 V 型起輔助定位夾緊作用。在通常情況下,過定位是不能使用的,但在某些特定情況下采用過定位方式能解決工件在機械加工中難以解決的一些問題 , 從而可獲得良好的加工效果 , 保證加工質量。
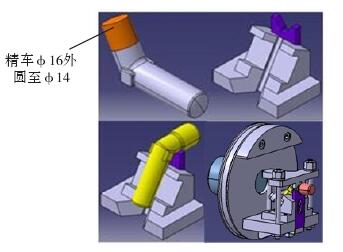
圖7 粗車毛坯一端外圓
2.2 粗車 Φ14 外圓
20 工序,粗車 Φ14 外圓至 Φ13。夾具設計如圖 8所示,用零件 15 工序車削外圓 Φ14 定位,120°夾角和活動 V 型塊定向的結構,其中活動 V 型塊可以調節夾具中心高,彌補中心偏移問題,且材料選為耐磨性好的 Cr WMn,方便磨損后更換。
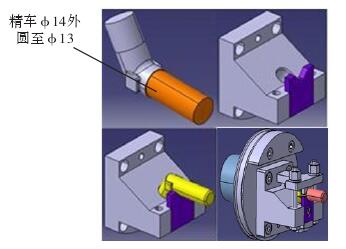
圖8 粗車毛坯另一端外圓
2.4 精車 Φ10 外圓
40 工序,精車 Φ10 外圓、鉆中心油路孔,夾具設計如圖 10 所示,用雙 V 型同時定位,雙面夾緊的結構,其中一個 V 型限制車削零件中心高,側邊 V 型起輔助夾緊作用,定位塊材料選用耐磨性好的 Cr WMn,保證工件定位準確、夾緊牢固,夾緊部位對主軸跳動量應控制在Φ0.03 內,車間使用非常穩定。
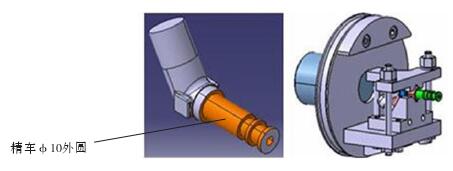
圖10 精車外圓面
2.5 精車螺紋
45 工序,精車 M12 螺紋、鉆中心油路孔,夾具設計如圖 11 所示,用零件 40 工序精車外圓 Φ10 作為主定位,零件 120°夾角定角向位置,15 工序粗車 Φ14 外圓為輔助定位,壓板采用圓弧形式,保證了零件定位、夾緊可靠。該夾具由主體、配重、定位板、壓板、螺釘、圓柱銷組成。在結構上,定位部分鑲入襯套,材料為黃銅,以免劃傷前道工序外圓表面,定位板和壓板均選用硬度高、耐磨性好的 Cr WMn 做為制造材料,且定位板用螺釘和圓柱銷連接在主體上,以便磨損后更換,夾具裝配時,夾緊部位對主軸跳動量應控制在 Φ0.03 內。經過本次工藝改進及工裝優化驗證,在車間加工過程中,未發生之前加工的質量問題,零件的尺寸都符合設計圖紙要求,滿足了產品的配套交付任務。
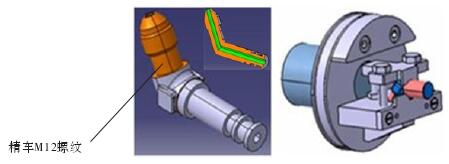
圖11 精車螺紋面
3 、車床夾具的模塊化實現
夾具模塊化實現過程是在進行各工序需求分析的基礎上,對其夾具結構形式進行評估,確定模塊化設計方案,主要包括專用模塊設計、通用模塊設計、模塊間組合[2]。首先進行專用模塊的設計,四道工序使用的車削夾具因基準選擇、定位方式不一樣,對其單獨進行結構設計,車床夾具主體、配重塊、壓板等可設計成通用模塊,便于相互間的互換,最后進行各模塊間的組合,形成最終夾具。
而目前以外圓或者內孔定位的車削工序,粗加工都是用三爪卡盤定位裝夾,三爪的自定心差,每次換爪都要重新找正,在半精加工或精加工定位一般采用軟爪定位裝夾,但是軟爪更換,需要重新鏜削軟爪,換裝、找正、調整時間長,效率低,另外三爪卡盤裝夾離心力大,無法獲得高轉速。
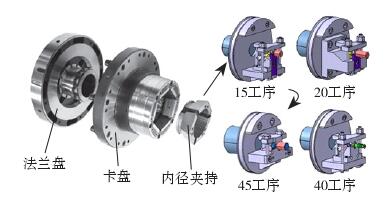
圖12 車床夾具快換過程
通過瀚柏格夾具快換系統實現車削夾具模塊間的快速更換。如圖 12 所示,車床主軸與法蘭盤連接,法蘭盤與卡盤連接,卡盤內預留標準接口實現內徑夾持、外徑夾持等,重復定位精度保證在 0.01 以內,實現各工序夾具模塊間的快速更換。經生產車間實際驗證,運用快換系統實現各工序間的加工能夠滿足工藝要求,做到機外裝夾工件,機床不停機加工,縮短了輔助準備時間,降低了工人勞動強度,提高了零件加工質量和生產效率。
4、結束語
通過對某管嘴零件車削加工的工藝優化及工裝設計,徹底解決了以往該零件加工多次返工,成批報廢的問題,車間生產過程中,零件加工質量穩定,效率明顯提升,一次合格率達 98 ﹪,為后續類似零件的加工提供了重要的參考依據。
投稿箱:
如果您有機床行業、企業相關新聞稿件發表,或進行資訊合作,歡迎聯系本網編輯部, 郵箱:skjcsc@vip.sina.com
如果您有機床行業、企業相關新聞稿件發表,或進行資訊合作,歡迎聯系本網編輯部, 郵箱:skjcsc@vip.sina.com