雙頭深孔槍鉆控制模型研究
2017-3-30 來源:湖北大學計算機與信息工程學院 作者:胡東紅,劉景源,張玲,王平江
摘要: 根據工件所需鉆孔的總排數、每一排的總孔數以及相鄰排之間的距離,按照最優的加工模式,自動確定雙頭鉆之間距離,自動確定鉆孔模式,并自動生成 G 代碼加工程序。提高鉆孔加工效率而且避免用戶繁雜的 G 代碼程序編寫和調試過程。
關鍵詞: 雙頭鉆; 深孔槍鉆; 鉆床; 數控中圖分類號: TP391 文獻標志碼: A 文章編號: 1671—3133( 2016) 03—0037—04
0.引言
鉆削直徑較小、深度較大的孔,尤其是在鋼件材料上鉆深孔、小孔時,通常存在鉆屑排除困難、刀具冷卻困難以及鉆孔軸線易歪斜等問題[1]。能否妥善解決這些問題,直接關系到深孔、小孔加工的質量、生產效率、加工精度和刀具熱變形等,若處理不當,甚至可能使加工無法正常進行[2-3]。對此類深孔、小孔問題,槍鉆是一個非常有效的解決方法[4-5],其主要特點是鉆頭中空細長,高壓鉆削油通過鉆頭中空管向鉆頭高速噴出,從而攜帶鉆屑從槍鉆的排屑槽向外噴出。深孔槍鉆無需通過反復拔出鉆頭的方式進行排屑,相對于麻花鉆有著無可比擬的優勢[6],從而提高了加工工效。此外,深孔槍鉆還采用鉆頭保護套,避免鉆頭歪斜。目前深孔槍鉆廣泛應用于汽車、模具、印刷機械、包裝機械、食品機械和航空航天等裝備制造領域的機械加工中[1]。此外,一些較復雜的工件排孔數很多,往往有幾萬個孔需要鉆削,如果采用單頭深孔槍鉆,加工一個工件往往需要晝夜 24 小時連續加工半個月左右。
雙頭深孔槍鉆的優勢在于可以用兩個鉆頭同時對工件進行鉆削加工,理論上講,可以節省加工時、提高加工工效近 50% 。但是,雙頭深孔槍鉆編程較為復雜,需要確定鉆孔模式。如果工件類型改變,排孔數發生變化,則需要重新進行編程、調試。用戶使用起來較為麻煩,因此,本文提出了雙頭深孔槍鉆的最優加工模式,可以根據工件的總排數、每排的孔數以及排間距等相關參數自動生成最優加工模式的 G 代碼程序。從而極大地簡化用戶的編程和調試。
1.問題描述
1.1 雙頭深孔槍鉆鉆床的主要結構
數控雙頭深孔槍鉆主要部件結構示意圖如圖 1 所示。左鉆頭和右鉆頭之間的距離可以通過手工調節后,保持固定。當左右鉆頭同時沿 X 軸方向移動時,可以分別同時對準圓筒工件上的兩排孔; 當工件繞 C 軸旋轉時,左右鉆頭可以分別對準圓筒工件上位于同一列的兩排孔; 當左右鉆頭同時沿 Z 軸移動時,左右鉆頭可以對圓筒工件上位于同一列的兩排孔進行鉆孔。
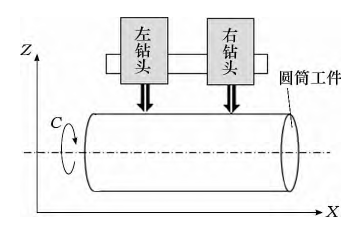
圖 1 雙頭深孔槍鉆主要部件結構示意圖
1. 2 最優化鉆孔模式要求
最優的雙頭深孔槍鉆鉆孔模式應該是: 盡量采用雙鉆模式進行鉆孔,即左右鉆頭同時鉆孔,以提高加工效率。若實在無法采用雙鉆模式鉆孔的孔位,采用單鉆模式鉆孔,即只用左鉆頭或只用右鉆頭鉆孔,因此,如何根據工件的總排數、每一排的總孔數以及排間距,自動確定左右鉆頭之間的距離,確定哪些排孔采用雙鉆模式,哪些排孔采用單鉆模式,是雙頭深孔槍鉆實現自動最優化鉆孔模式的關鍵所在。
2.雙頭深孔槍鉆最優鉆孔模式分析
一個圓筒工件及其展開后的排序號和孔序號示意圖如圖 2 所示。由于奇數排的孔和偶數排的孔沿 X軸線方向不在一條直線上,且相互錯位半個孔間距,因此,左鉆頭和右鉆頭無法分別鉆奇數排的孔和偶數排的孔。左鉆頭和右鉆頭只能同時鉆奇數排的孔,或者同時鉆偶數排的孔。
如圖 3 所示為工件總排數為 8 排時的鉆孔模式。如果工件的總排數為 8 排,顯然,最合理的鉆孔模式是左鉆頭和右鉆頭的間距為孔的排間距的 4 倍最為合理。這樣,左鉆頭對準第 1 排時,右鉆頭對準第 5 排。在左右鉆頭同時完成對第 1 排和第 5 排的全部鉆孔之后,左右鉆頭分別對準第 2 排和第 6 排,同時完成第 2排和第 6 排的全部鉆孔。同理,左右鉆頭可以同時完成第 3、7 排,第 4、8 排的全部鉆孔。可以將該過程描述為: 用雙鉆模式,第 1 輪完成對第 1、5 排的鉆孔; 第2 輪完成對第 2、6 排的鉆孔; 第 3 輪完成對第 3、7 排的鉆孔; 第 4 輪完成對第 4、8 排的鉆孔。一共進行 4輪鉆孔,所花時間相當于鉆 4 排孔的時間。
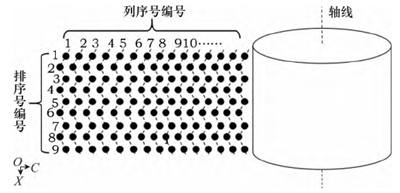
圖 2 圓筒工件展開后的排序號和孔序號示意圖
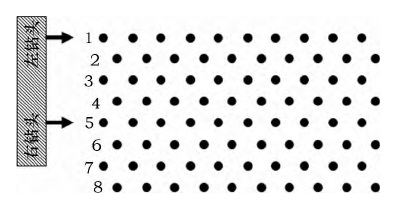
圖 3 工件總排數為 8 排時的鉆孔模式
如果工件的總排數為 9 排時,顯然,最合理的鉆孔模式是: 按照總排數為 8 排的模式,完成對 8 排孔的鉆孔之后,拆掉一個鉆頭,用剩下的一個鉆頭進行第 5 輪鉆孔,完成對第 9 排全部孔的鉆孔。一共進行 5 輪鉆孔,所花時間相當于鉆 5 排孔的時間。
如果工件的總排數為 10 排,顯然,最合理的鉆孔模式是: 按照總排數為 8 排的模式,完成對 8 排孔的鉆孔之后,拆掉一個鉆頭,用剩下的一個鉆頭進行第 5輪、第 6 輪鉆孔,完成對第 9、10 排全部孔的鉆孔。一共進行 6 輪鉆孔,所花時間相當于鉆 6 排孔的時間。
但是,當工件的總排數為 11 排時,如果仍然按照總排數為 8 排的模式,完成對 8 排孔的鉆孔之后,拆掉一個鉆頭,用剩下的一個鉆頭進行第 5、6、7 輪鉆孔,完成對第 9、10、11 排全部孔的鉆孔。這樣一共進行 7 輪鉆孔,所花時間相當于鉆 7 排孔的時間。事實上,當工件的總排數為 11 排時,最合理的鉆孔模式是: 左右鉆頭的間距設定為孔的排間距的 6 倍,圖 4 所示為工件總排數為 11 排時的最優鉆孔模式。這樣,左鉆頭對準第 1 排時,右鉆頭對準第 7 排。鉆孔過程可以描述為:用雙鉆模式,第 1 輪完成對第 1、7 排鉆孔; 第 2 輪完成對第 2、8 排鉆孔; 第 3 輪完成對第 3、9 排鉆孔; 第 4 輪完成對第 4、10 排鉆孔; 第 5 輪完成對第 5、11 排鉆孔;第 6 輪拆掉一個鉆頭,用一個鉆頭采用單鉆模式完成對第 6 排的鉆孔。這樣一共進行 6 輪鉆孔,所花時間相當于鉆 6 排孔的時間。
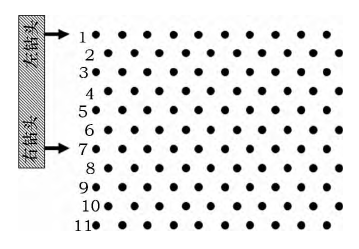
圖 4 工件總排數為 11 排時的最優鉆孔模式
從上述分析可以看出,工件總排數為 4 的整數倍,即 4n( n = 1,2,…) 時,左右鉆頭的間距應該為排間距的 2n 倍。一共進行 2n 輪雙鉆模式鉆孔。總排數為4n 時的最優鉆孔模式如表 1 所示。
表 1 總排數為 4n 時的最優鉆孔模式
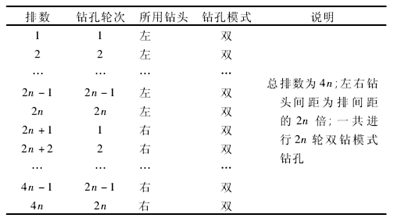
工件總排數為 4 的整數倍余 1,即 4n + 1,( n = 1,2,3,…) 時,左右鉆頭的間距應該為排間距的 2n 倍,鉆孔的輪次數 2n + 1 輪次。其中 2n 輪次為雙鉆模式,1 輪次為單鉆模式,總排數為 4n + 1 時的最優鉆孔模式如表 2 所示。
表 2 總排數為 4n + 1 時的最優鉆孔模式
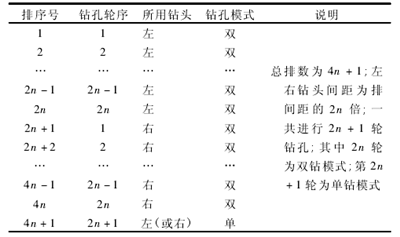
工件總排數為 4 的整數倍余 2,即 4n + 2,( n = 1,2,3,…) 時,左右鉆頭的間距應該為排間距的 2n 倍,鉆孔的輪次數 2n + 2 輪次。其中 2n 輪次為雙鉆模式,2 輪次單鉆模式。總排數為 4n + 2 時的最優鉆孔模式如表 3 所示。
表 3 總排數為 4n + 2 時的最優鉆孔模式

當工件總排數為 4 的整數倍余 3,即 4n + 3,( n =1,2,…) 時,左右鉆頭的間距應為排間距的 2n + 1 倍,鉆孔的輪次數 2n + 2 輪次。其中( 2n + 1) 輪次為雙鉆模式,1 輪次為單鉆模式。總排數為 4n + 3 時的最優鉆孔模式如表 4 所示。
表 4 總排數為 4n + 3 時的最優鉆孔模式
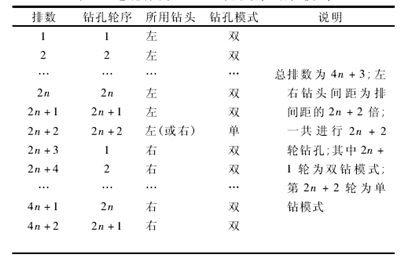
3.結語
根據上述雙頭深孔槍鉆最優鉆孔模式算法,在華中 21 型數控系統平臺上進行二次開發,實現了本方案的應用。用戶只需輸入工件的總排數、每排的孔數、排間距和鉆孔時的速度等相關參數,數控系統即可自動生成最后的鉆孔加工程序,從而極大地簡化了用戶的編程和調試。
加工后尺寸精度難以把控的特點,創新性地提出了運用五軸聯動數控砂帶磨床對其表面進行高效高精度打磨,機床的工藝靈活性與加工適應性均得到了較高程度的提升。最后進行了實際加工實驗,結果證明葉片型面磨削效果與磨削效率遠高于現階段高強度且磨削質量難以管控的手工作業方式。
2) 本文在不犧牲數控砂帶磨床原有加工效率的前提下優化了磨削工具進入葉根圓角難加工區域的位姿形態,使磨削工具的可達磨削區域得到了一定程度上的提升。
投稿箱:
如果您有機床行業、企業相關新聞稿件發表,或進行資訊合作,歡迎聯系本網編輯部, 郵箱:skjcsc@vip.sina.com
如果您有機床行業、企業相關新聞稿件發表,或進行資訊合作,歡迎聯系本網編輯部, 郵箱:skjcsc@vip.sina.com
更多相關信息