薄壁零件的數控車削
2020-5-1 來源: 韶關市乳源瑤族自治縣中等職業技術學校 作者:崔 毅
摘要:薄壁零件的加工由于夾緊力、車削力、車削熱、內應力、振動與變形等因素的影響,使工件產生較大的變形,導致零件的加工質量難以保證。筆者從工件的裝夾、刀具要求、程序的編制等方面進行綜合考慮,解決了薄壁零件的車削加工難題,從而有效提高了零件的精度,保證了產品的質量。
關鍵詞 : 薄壁零件 車削加工 夾具 程序
薄壁零件因其結構緊湊、質量輕、節省材料等特點,在各工業部門日益得到廣泛應用。但由于薄壁零件強度低剛性差,加工過程中極易變形,難于保證零件的加工精度,所以薄壁零件加工難成為一個凸顯的問題。下面以某型號產品的一薄壁套筒為例,對薄壁零件的數控車削加工工藝進行研究。
1、 影響薄壁零件加工精度的主要因素
影響薄壁零件加工精度的因素有很多,但歸納起來主要有以下三個方面:
1.1 易受力變形
因壁薄,在夾緊力的作用下,容易產生變形,從而影響工件的尺寸精度和形狀精度。如圖1 所示。
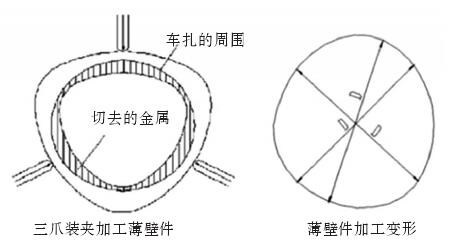
圖 1 工件振動變形
1.2 易受熱變形
因工件較薄,切削熱會引起工件熱變形,使工件尺寸難以控制。
1.3 易振動變形
在切削力 (特別是徑向切削力) 的作用下,容易產生振動和變形,影響工件的尺寸精度和形狀、位置精度和表面粗糙度。
2 、薄壁零件加工案例分析
如下圖 2 所示,是企業接單生產的薄壁零件。為了提高產品的合格率,我們從工件的裝夾(夾具的設計加工)、工藝路線分析、刀具幾何參數、切削用量等方面進行綜合考慮。實踐證明,有效提高零件的精度,保證了產品的質量,提高了生產效率,為企業贏得了經濟效益。
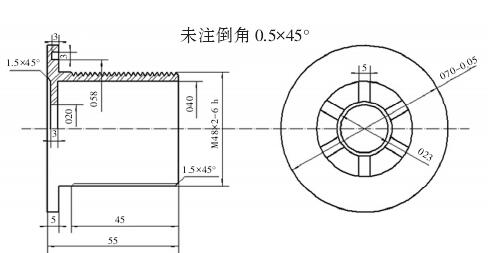
圖 2 薄壁零件
2.1 圖樣、毛坯及加工難點的分析
2.1.1 圖樣分析 該零件是一個套類薄壁零件,左端為一個70 mm、 厚度為 5 mm 的薄大凸外圓,在外圓右端面上有一 58 mm、寬度和深度都為 3 mm 的端面槽,左端中間由壁寬為 5 mm、厚為 3 mm 的六塊肋板組成,肋板中間有 20 mm、厚為 1.5 mm 的圓孔。零件右端為一個圓筒,壁厚為4 mm, 在48 mm 的圓筒外圓面上加工有M48 × 2 的三角螺紋,整個零件的工藝倒角為 0.5× 45°,總長為 55 mm。
2.1.2 零件毛坯分析 毛坯是由生產廠家鑄造成型的粗坯,材料為 45#鋼,需要加工零件的外圓、端面、端面槽和螺紋部分,其中螺紋是加工重點,每個面的加工余量小,只有 0.5~1 mm,而加工的批量又較大。
2.1.3 從零件圖樣要求及材料分析 加工此零件的難度主要有兩點:①主要因為是薄壁零件,材料為 45#鋼,批量較大,既要考慮如何保證工件在加工時的定位精度 , 又要考慮裝夾方便可靠。而我們通常都是用三爪卡盤夾持外圓或撐內孔的裝夾方法來加工。但此零件較薄,車削受力點與夾緊力作用點相對較遠 , 還需車削M48 × 2 螺紋,受力很大,剛性不足,容易引起
晃動 。 因此要充分考慮如何裝夾和定位的問題。②螺紋加工部分厚度只有 4 mm,而且精度要求較高。
2.2 夾具的設計
2.2.1 右端外圓的裝夾設計 此端為薄壁,厚度為 4 mm。從圖 3 中可以看到零件是在三爪自定心卡盤上裝夾 , 零件只受到三個爪的夾緊力,夾緊力不均衡,會出現圖 1 的情況,使零件變形。如圖 4 所示,采用開縫套筒裝夾,增大零件的裝夾接觸面,零件的變形小,此方法可行。
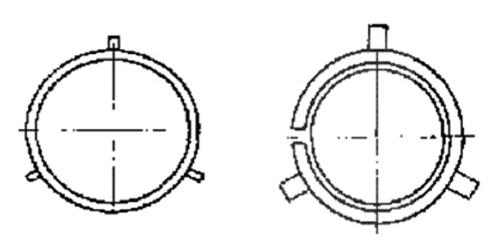
圖 3 三爪自定心卡盤裝夾 圖 4 開縫套簡裝夾
2.2.2 裝夾采用的辦法 對于毛坯上 5 mm 凸圓的右端面以及端面槽、右端外圓和螺紋的車削,裝夾采用的辦法就是先在卡盤的三個卡爪上按要求車削一個直徑為80 mm、 深度為 2 mm 的圓孔。之后,分別焊接一個扇型凸臺,凸臺厚度為5 mm,將卡爪改進成如圖 5 所示的情況,用來夾住零件的左端,然后在零件的右端設計一個專用夾具如圖 6 所示,把其放入內孔中,用來固定并頂住零件右端,從而形成一夾一頂的牢固裝夾,其裝夾示意圖如圖 7 所示。當加工完成后,右端專用夾具可從零件內孔抽出,如圖 8 所示,從而完成零件的裝卸。
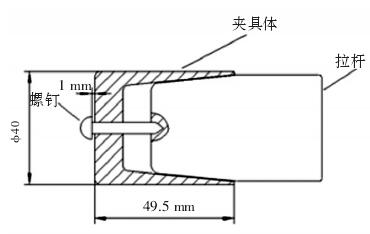
圖 5 卡爪改進
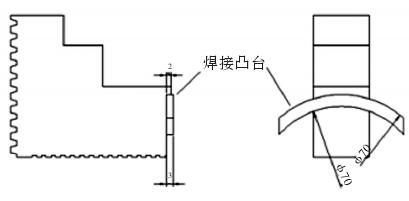
圖 6 專用夾具
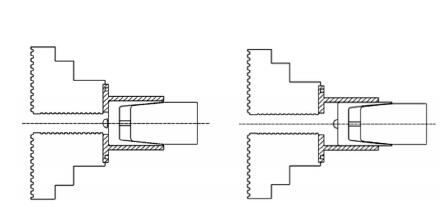
圖 7 裝夾示意 圖 8 專用夾具
2.3 加工工藝的制訂
2.3.1 螺紋的加工工藝分析 螺紋的加工是該零件的重點和難點,加工部分厚度只有 4 mm,而且精度要求較高。在加工螺紋的時候,要非常的小心,加工螺紋的切削速度和進給量都要充分考慮。另外,數控加工螺紋的指令也要選擇恰當,可以根據工件的具體情況,分析一下采用哪種程序指令進行螺紋的數控加工。
FANUC 數 控 系 統 螺 紋 編 程 指 令 有 G32、G92、G76。G32 是簡單螺紋切削,顯然不適合。G92 螺紋切削循環采用直進式進刀方式,刀具兩側刀刃同時切削工件,切削力較大,而且排屑困難。因此在切削時,兩切削刃容易磨損。從以上對比可以看出,只簡單利用一個指令進行車削螺紋是不夠完善的,采用 G92、G76 混用進行編程,即先用 G76 進行螺紋粗加工,再用 G92 進行精加工,在薄壁螺紋加工中,將有兩大優點:一方面,可以避免因切削量大而產生薄壁變形。另一方面,能夠保證螺紋加工的精度。
2.3.2 合理安排加工工藝路線 (見下表)。
合理安排加工工藝路線表
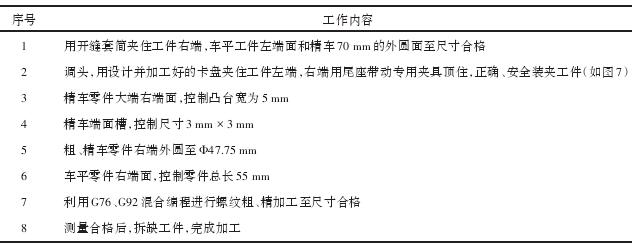
2.3 加工工藝
2.4 刀具的選擇
該企業所用數控車床與高速鋼刀具都是從外國進口的,其質量與性能都能得到保證。在薄壁零件的車削中,合理的刀具幾何角度對車削時切削力的大小,車削中產生的熱變形、工件表面的微觀質量都是至關重要的。刀具前角大小決定著切削變形與刀具前角的鋒利程度。前角大,切削變形和摩擦力減小,切削力減小。但前角太大,會使刀具的楔角減小,刀具強度減弱,刀具散熱情況差,磨損加快。所以,一般車削鋼件材料的薄壁零件時,用高速鋼刀具,前角取 6°~30°,用硬質合金刀具,前角取 5°~20°。
2.5 切削參數的選擇
薄壁零件車削時變形是多方面的,裝夾工件時的夾緊力、切削工件時的切削力、工件阻礙刀具切削時產生的彈性變形和塑性變形,使切削區溫度升高而產生熱變形。所以粗加工時,背吃刀量和進給量可以取大些;精加工時,背吃刀量一般在 0.2~0.5 mm,進給量一般在 0.05~0.1 mm/r,甚至更小,切削速度 60~120 mm/min,不宜過高。根據切削用量的選用原則,合理的確定數控車床的各項切削參數 : ① 粗車時 , 主軸轉速600~800 r/min,進給速度 F120~F160,留精車余量 0.3~0.5 mm。②精車時,主軸轉速 1 200~1 500 r/min,進給速度 F60~F80,采用一次走刀完成。③螺紋加工時,用 G76 粗車完成后,留給精車余量 0.1~0.2 mm, 再用 G92 指令精車三次,主軸轉速 500 r/min
2.6 切削液的選擇
在車削薄壁工件時 , 切削液是必不可少的, 應根據加工材料、加工性質和刀具材料等具體情況選用適當的切削液, 才會更有利于加工的進行。該企業他們統一用專用的冷卻油,冷卻效果明顯,對工件和刀具的潤滑作用很好。最后,進行科學編程并進行單件試制加工后調整,再批量生產。
3 、加工時的注意事項
①要遵守安全操作守則,安全文明生產。
②工件要夾緊,以防在車削時打滑飛出傷人和扎刀。
總之,通過實際加工生產,以上措施很好地提高了薄壁零件的加工精度,減少了工件裝夾與校正的時間,降低了操作者的勞動強度,提高效率并保證加工后零件的質量,經濟效益十分明顯。
投稿箱:
如果您有機床行業、企業相關新聞稿件發表,或進行資訊合作,歡迎聯系本網編輯部, 郵箱:skjcsc@vip.sina.com
如果您有機床行業、企業相關新聞稿件發表,或進行資訊合作,歡迎聯系本網編輯部, 郵箱:skjcsc@vip.sina.com
更多相關信息