一種變速箱加工的數控系統設計與實驗研究
2020-7-6 來源: 陜西工業職業技術學院 作者:鄧豐曼
摘要:針對傳統的多軸數控機床較難滿足變 速箱加工過程中精度要求,提 出了一種基 于 “ARM+DSP”硬件結構的參數可重構嵌入式數控系統的設計。所設計的數控系統通過參數化自動編程模塊,實現了根據變速箱齒輪的參數、加工刀具參數和加工過程參數自動生成數控加工程序,還能夠通過專家數據庫優化數控程序中周期性參數的設置,同時在所設計的數控系統中應用了一套新型的軟件電子變速器,以達到提高多軸同步運動控制精度的目的。實驗結果表明,將所設計的嵌入式數控系統應用于六軸滾齒機,能夠有效提高變速箱齒輪的加工精度。
關鍵詞:變速箱;嵌入式數控機床;參數自動編程;專家數據庫;電子齒輪箱
0引言
變速箱是機械設備的重要基礎部件,廣泛用于船舶,汽車,飛機,農業設備,工程機械,采礦設備和電力設備等。變速箱對加工精度要求較高,通常使用數控機床實現對變速箱的高精度加工。數控機床的多軸同步運動的控制精度是影響變速箱加工精度的主要因素[1-3]。傳統的數控機床都使用機械傳動鏈來控制直線運動和旋轉運動,以實現運動軸的準確跟隨運動[4-6]。因此傳動鏈上每個部件的磨損、熱偏轉、參數設置誤差都會降低連續運動精度[7-8]。
一些研究成果表明,利用嵌入式系統的巨大運算能力能夠有效補償機床動態誤差,提高數控機床的控制精度。文獻[8]中提出了一種基于關鍵實時任務輸出抖動的模糊反饋調度算法,以解決嵌入式系統實現中,由系統資源和處理器使用限制引起的不確定性因素。文獻[9]將可重構邏輯被應用在高速CNC數字控制器中,以滿足數控機床中伺服回路的實時性要求。文獻[10]在CNC中利用以太網Power-link通信總線實現了控制組件接口在實時操作系統下運行。文獻[11]針對不同的應用領域,基于嵌入式技術引入了一些專用數控系統硬件和軟件結構。該研究表明,與通用機床相比,專用機床對齒輪等特殊部件的加工具有效率高和精度好的優點。基于上述研究,在傳統數控系統中引入嵌入式硬件平臺,開發了變速箱加工專用數控系統。該系統基于變速箱齒輪加工工藝的特點,設計出具有柔性加工功能的電子齒輪箱(EGB)功能模塊,以充分適應不同變速箱齒輪加工 工藝 的要求。該系 統 通過參數化自動編程,實現自動生成加工數控程序的功能。并利用專家數據優化加工參數,提高數控程序的可靠性。最后通過實驗對所設計的數控系統的有效性進行驗證。
1、硬件平臺和軟件框架
對于高性能嵌入式數控系統而言,數控系統開發人員可以將新技術集成起來,具有很強的適用性和開放性,用戶可以輕松地 進行二次開發,擴 展 系統的功能。根據實際加工要求,可以將結構切割成各種齒輪加工數控系統[12-14]。本文的ARM和DSP組成的數控系統的硬件結構如圖1所示。
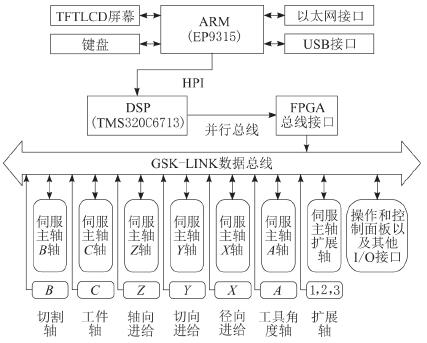
圖1數控系統平臺的硬件結構
2個芯片的型號分別為 ARMEP9315和DSPTMS320C6713。DSP芯片完成復雜的數學運算和實時任務,包括位置控制,插值計算和 PLC 控制。ARM 芯片完成人機交互和界面管理,如代碼編程,參數設置和狀態顯示。系統前臺 ARM 與后臺DSP之間的數據交換通過HPI實現。
完整的數控系統包括各種類型的任務:周期性的實時任務,如位置控制、插補計算和 PLC控制;非周期性的實時任務,如系統狀 態 顯示、報 警檢測和數據交換;非實時任務,如參數管理、代碼編譯和文件管理。 實時任務具有并發性特征,并且同時執行。因此,需要一個實時操作系統(RTOS)來管理和調度多 任務環 境中的實 時 任務[15-16]。為 了完成數控系統,除了硬件結構之外,還應該設計軟件。
圖2所示的軟件分為前臺系統軟件和后臺軟件2部分,運行在具有不同工作頻率和不同處理器的內存上。通過使用不 同的芯 片 可以充分 發揮其優點,從而獲得高性能。將 WinCE 操作系統移植到具有強大事務管理能力的ARM內核。ARM 芯片上運行的應用軟件 包括參數 管理、文件管 理、狀態和報警信息顯示、自動編程和圖形模擬功能。內核層實時控制軟件運行在DSP(
TMS320C6713)上,BIOS部署在DSP內核上,以獲得較高的控制精度。控制軟件主要由3個周期性實時任務:位置控制;插補和PLC控制組成,其運行周期分別設置為0.25
ms,1ms和10ms。

圖2數控系統的軟件架構
2 、參數化自動編程
參數化智能自動編程功能模塊的結構如圖3所示。用戶只需設置齒輪參數(如齒輪類型,齒輪特征參數),刀具參數(如刀具類型,刀具特征參數 )和切削循環參數。然后通過自動編程模塊獲取加工程序,通過圖形仿真驗證NC代碼的正確性。齒輪可以加工包括圓柱齒輪,鼓齒輪,小錐齒輪,非圓齒輪,螺旋錐齒輪和齒條。特征參數包括齒數、模數、壓力角、螺旋角和齒寬等。不同齒輪對象的刀具參數不同。生成并通過動態驗證后,加工代碼將通過 HPI下載到指令緩沖區,數據結構可由 DSP識別。這些代碼將在DSP中得到執行。通過編譯預處理,加減速實時處理,插補實時計算得到用于控制機床軸運動的實時位置控制數據。根據插補數據,齒輪輪廓將被加工。
在獲得加工代碼之前,可以通過手動模式或自動查詢模式輸入切削參數。在過程數據庫的支持下,可以自動選擇切削參數,如主軸轉速、進給速率和切削方式。對于具有不同力學性能的各種齒輪,使用專家知識選擇的參數將是最佳的,并且它們將提供最理想的精度和效率。
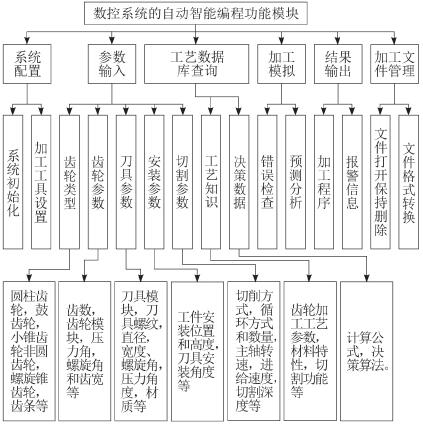
圖3智能自動編程模塊的軟件體系結構
3、變速箱加工工藝專家數據庫
齒輪加工過程數據庫是一個數據管理軟件,包括齒輪刀具信息,齒輪零 件信 息 和切削過程信息。它具有數據定義、數據輸入、數據修改、數據 刪除、數據查詢、數據輸出、數據管理和數據分析等功能,為齒輪加工提供幫助。該數 據庫主要由用戶前臺操作界面和后臺數據操作功能組成,作為功能模塊內置于數控系統軟件中。其結構如圖4所示。
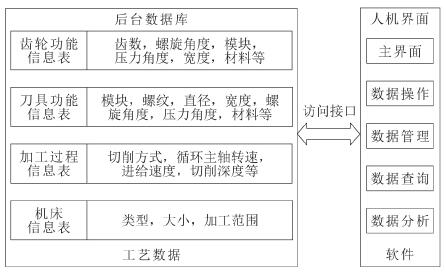
圖4變速箱加工工藝專家數據庫功能模塊
數據和模型是專家數據庫系統的2個重要組成部分。數據是變速箱加工的基礎信息,數據模型是獲得最佳切削工藝參數的分析方法。在數據庫中,通過加工過程手冊,實驗和實際生產收集數據。采用關系模型分析齒 輪、刀具、機床 和 切削工藝參數的相關性。與網絡模型和層次模型相比,關系模型的結構簡單,并且使用二維關系表來描述實體之間的關系。它基于嚴格的數學基礎,每個屬性又是不可分割的,因此可以更好地保證數據的完整性和數據的一致性。
變速箱加工過程 數 據庫設計工作主要包括需求分析,概念設計,結構設計和物理設計。根據齒輪加工應用要求,首 先要建立齒 輪特征信息表,切削刃特征信息表,切削過程參數表,機床信息表。主要特征需要包含在這些表格中,以便獲得最佳結果。物理設計是在系統資源的限制下,開發適合嵌入式數控系統的存儲結構和方法。對于所提出的硬件結構,數據庫是通過基于SQLite3的Visual Studio VC ++編程環境進行設計和開發的。如前所述,CNC內置的數據庫可以支持自動編程模塊以獲得最佳加工程序。此外,還可以用來為技術人員提 供 一個獨立 模 塊的指導。對于用戶來說,它可以帶來足夠 的 便利來保 存、管理和優化加工參數。同樣,系統也可以通過積累加工大數據來實現智能化數控加工。
4 、高精度軟件電子變速箱
電子齒輪 箱 (EGB)通過高性 能 微處理器取代了機械傳動鏈,大大提高了機械系統的靈活性和傳動精度。EGB軟件是用來取代復雜的硬件邏輯電路,任何傳動率都可以在理論上被 EGB所實現。值得注意的是,數控系統的穩定性和靜態誤差并沒有在EGB中得到有效解決。對于變速箱加工,變速齒輪形狀可以通過刀具主軸、工件主軸和進給軸的同步運動形成。變速箱齒輪加工精度主要取 決 于同步精 度。為 了實現多軸同步,采用了復合結構 EGB。在 EGB中,根據安裝在刀軸上的編碼器的反饋數據和其他進給軸的指令數據,計算出從動軸 的 下列位置 和 速 度指令。然后,所有軸的實時指令被發送到位置控制器以驅動這些軸。每種齒輪加工方法都對應于 EGB結構。
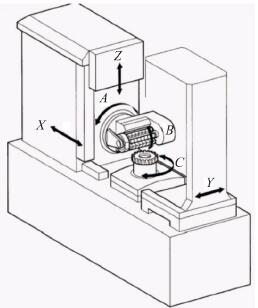
圖5滾齒機的整體結構
提出了適用于齒輪加工數控系統的齒輪銑削,成型、滾銑、磨削和研磨加工過程的 EGB。在此,將闡述用于變速箱滾齒的EGB。滾齒機的整體結構如圖5所示。圖5中,滾刀主軸B、工件主軸C 和軸向進給軸Z是最上面的成形運動軸。Y 是用于更換刀片的滾刀末端軸。X 是實現全齒深切的徑向進給軸。A 是滾刀安裝角度調整軸,它是具有不同螺旋角度的齒輪的變體。C 軸主要跟隨滾刀軸B 的運動,B 與C 之間的關系滿足:

nB為滾刀主軸B的速度;nC為工件主軸C的跟隨速度;ZB為滾刀的螺紋數;ZC為工件齒輪的齒數;KB的值是根據旋轉滾刀主軸的方向來確定。當變速箱齒輪達到設計齒寬時,滾刀需要沿進給軸Z移動,此時在C軸上增加一個額外的運動,可以根據Z軸的行程距離獲得附加的值。類似地,當采用對角線滾邊加工方法時,Y 軸引起附加的運動。在C軸上的附加運動值為:

ΔθC是由Z軸和Y軸引起的附加移動;Δz是Z軸的移動距離;Δy是Y軸的移動距離;ZC是齒輪齒數;β為加工齒輪的螺旋角;λ為滾刀安裝角度;KZ和KY的值根據β,Δz和 Δy
分別取“+1”或“-1”。結合式(1)和式(2),滾刀 EGB同步關系為:

θC,θB,z和y分別表示C 軸的跟隨角度位置、滾刀主軸的移動角度位置、Z 軸的移動距離和Y 軸的移動距離。θB,z和y 的值可以從插值結果中獲得,因此只需要定義ZB,ZC
,mn,β和λ的指令在內的指令即可通知CNC系統,并且θC可以是自動獲得。特殊代碼G81定義為打開EGB并限制所有機床軸的運動關系。G80被 定義為關閉EGB并取消同步約束。
當EGB有效時,C軸隨動Y 軸、Z軸和B 軸的運動,其關系符合式(3)。如果 G81無效,C 軸將是一個通用軸。因此,變速箱數控加工系統也可以作為傳統的通用數控系統,如車床、銑床和加工中心。EGB的實現過程如圖6所示。
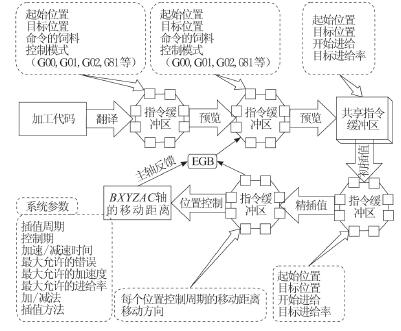
圖6EGB的實現過程
當檢測到EGB指令時,同步數據信息被存儲在環形指令緩沖器中。最 終的位置 控 制數據被發送到位置控制器以驅動機床,在預見計數過程,加速/減速控制,粗略插補和精細插補之后。被存儲在環形指令緩沖器中。最 終的位置 控 制數據被發送到位置控制器以驅動機床,在預見計數過程,加速/減速控制,粗略插補和精細插補之后。
5 、性能驗證
所提出的關鍵技術在水平六軸 滾齒機的滾齒試驗中得到驗證。該滾齒機用內部開放式嵌入式齒 輪加工數控系統,采用 “ARM + DSP”硬件結構。滾齒機實驗平臺的整體結構如圖7所示。
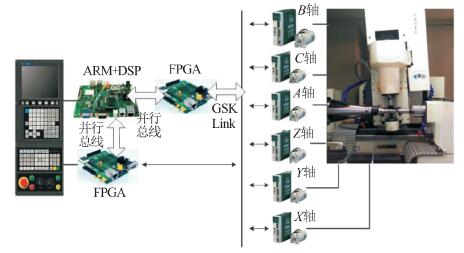
圖7 實驗平臺的整體結構
所有軸均由交流伺服電機驅動,其控制方式為速度控制方式。數控 系統的 硬 件和軟件 結構在前一節中介紹。數控系 統的主 要 功能是精 確控制機床完成滾齒,包括加工程序生成、信息管理、機床監控狀態顯示、發送運動控制指 令、接收反 饋信息控制滾齒機。表1總結了伺服電機參數以及每個機床軸的機床結構參數。
表1每個機床軸的伺服電機和結構參數
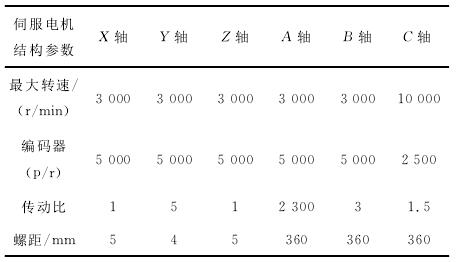
進給和主軸伺服編碼器分別產生2000和1000個脈沖,而編碼器信號通過四倍頻電路進行細分。數控系統基于 使用右向滾刀加工右軸齒輪進行性能測試。對變速箱齒輪進行機械加工時,主軸轉速達到1000r/min,并分別以10mm/min和5mm/min的軸向和徑向進給速度進行切削。表2給出了待加工變速箱齒輪的參數和相應使用的滾刀參數。
表2實驗齒輪和刀具參數
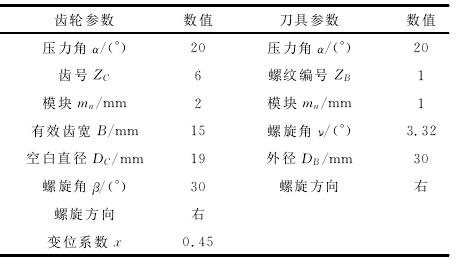
5.1空氣切割實驗
在自動編程功能模塊中輸入這些參數后,將自動生成加工代碼。采用 軸向 滾齒加工方法來驗證變速箱齒輪加工數控系統的有效性。
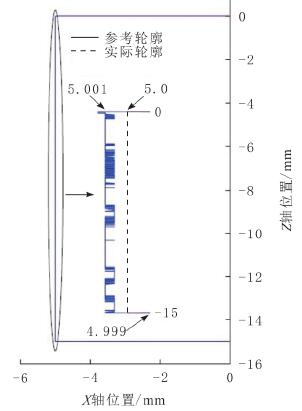
圖8 X-Z平面參考與實際輪廓
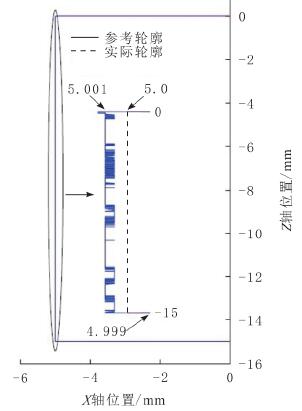
圖9 C軸理論與實際位置
在測試過程中,記錄和比較關節軸所需的指令信號和編碼器反饋信號。X 軸、Z 軸和C 軸的理論和實際輪廓分別如圖8和圖9所示。對圖8和圖9中的實驗加工結果進行分析,可以看出,所有的理論位置和實際位置都略有不 同,但是每個軸都能夠精確地跟隨位置指令。實 驗 中工件的測量值滿足式(1)和式(2)的同步控制要求。
實驗中X軸和Y軸的編碼器的脈沖分辨率為0.25μm,C軸編碼器的脈沖分辨率為0.006°。整個軸向滾齒加工過程數控系統 的X軸 和Z軸平均跟蹤誤差 都 小于0.75μm,C 軸 平 均 跟 蹤 誤 差 為0.0153°,這些誤差都分別小于對應的編碼器脈沖。很顯然,實驗數控平臺能夠滿足變速箱加工的精度要求,可以用來實現變速箱的齒輪高精度加工。對于用于變速箱加工的多軸輪廓控制系統,輪廓誤差都是評估控制系統性能的重要評估指標。輪廓誤差有螺旋偏差和螺距偏差2方面。
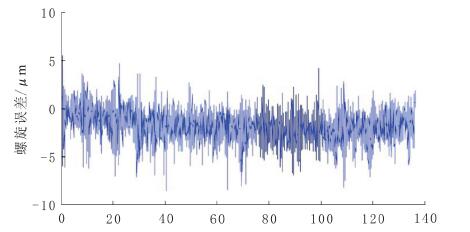
圖10 螺旋誤差
由圖10可知,螺旋誤差的最大值為9.5μm,平均螺旋誤差為1.8μm,可以達到變速箱加工的要求。
從圖10可以清楚地看到,參與切削過程的各軸跟蹤誤差足夠小,可以證明實驗數控平臺的跟蹤控制性能。因為齒輪螺旋線是由 Z 軸進給,工件主軸C軸和滾刀主軸B軸使用軸向滾齒方法同步運動而產生的。因此,齒輪加工精度不僅取決于C軸的跟蹤性能,而且還取決于所有軸的同 步輪廓控制性 能。圖11和圖12分別分析了變速箱齒輪加工的節距誤差和螺旋誤差。圖11中分析的螺旋誤差可以滿足變速箱齒輪切削的精度要 求。下一步將通過變速箱齒輪加工實驗進一步說明數控系統的性能。
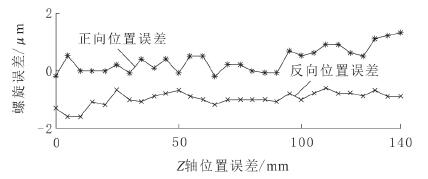
圖11 Z軸位置誤差/mm
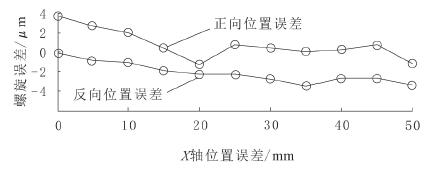
圖12 X軸位置誤差/mm
5.2 變速箱齒輪加工測試
在加工測試之前,嵌入式變速箱齒輪加工數控系統的性能通過前面提到的軸向滾齒方式進行驗證。在變速箱齒輪加工之前,由于滾齒機采用了半閉環位置控制模式,因此使用激光干涉儀檢測位置精度,并通過數控系統的螺距誤差和齒隙補償功能進行補償。圖11和圖12中顯示了2個主直軸的位置誤差測量結果。結果表明,機床位置誤差完全滿足要求并且范圍較小。參數如表2的齒輪和刀具用于加工實驗。40Cr工件以4.5mm的切削深度一次切削循環切削。切割后,使用齒輪精度測試中心測量螺距誤差和螺旋誤差。從測試結果來看,左齒面的最大誤差為6.3μm,右齒面的最大誤差為5.1μm,滿足設計要求。
6、結束語
提出了一個具 有可重構參數的 數控系統。變速箱齒輪數控加工系統可以通過簡單的參數設置用于不同的加工機床。介紹 了應用于變速箱加工數控系統的關鍵技術,這些技術包括參數化智能自動編程、專家數據庫和高精度 EGB。該系統的軟件結構是在“ARM + DSP”硬件平臺上構建和實現的。為了驗證這些功能的有效性,實驗在具有內部嵌入式數控系統的六軸臥式滾齒機上進行了空氣切割狀態和實際加工 測 試。實驗 結果證明了系統能夠有效地應用于變速箱的加工。
雖然所提出變速 箱 齒輪數控 系 統可以滿足變速箱齒輪加工的要求,但齒輪的每個齒輪的輪廓誤差存在一定的波動范 圍。由于輪廓誤差可以通過實時預補償解決方案加以提高,因此下一步的研究是基于預補償控制算法進一步提高 數控系統的加工性能。
投稿箱:
如果您有機床行業、企業相關新聞稿件發表,或進行資訊合作,歡迎聯系本網編輯部, 郵箱:skjcsc@vip.sina.com
如果您有機床行業、企業相關新聞稿件發表,或進行資訊合作,歡迎聯系本網編輯部, 郵箱:skjcsc@vip.sina.com
更多相關信息