TA2 表面電火花沉積 Zr / WC 復合涂層特性及界面行為研究
2017-3-22 來源:河南科技大學 作者:吳公一,張占領,孫凱偉,于華,邱然鋒,石
摘要: 目的通過在 TA2 表面進行電火花沉積改變其表面性能。方法 采用電火花沉積技術,在基體TA2 表面制備 Zr / WC 復合涂層,然后分別用掃描電鏡( SEM) 、能譜分析儀( EDX) 、X 射線應力分析儀、顯微硬度計和摩擦磨損試驗機分析涂層的微觀組織、化學成分分布、殘余應力、顯微硬度分布以及涂層的耐磨性。結果 復合涂層連續、均勻,厚度約為 50 ~ 80 μm; 涂層表面不平整,存在很多小坑和粘連,涂層內部有少量氣孔和裂紋; 復合涂層與基體的主要元素 Ti、Zr、W 之間發生相互擴散,并發生冶金反應; 經過電火花沉積后 TA2 表面存在較大的殘余應力,通過改變工藝參數可有效控制殘余應力; 復合涂層表面顯微硬度值最高能達到 960. 5HV200g,約為基體的 4 倍; 經過電火花沉積 Zr/WC 復合涂層的試樣磨損量遠遠小于 TA2 試樣,εw= 4.1,沉積層的耐磨性比基體材料提高了3.1倍,經電火花沉積制備復合涂層后表面的耐磨性顯著提高。結論 在 TA2 表面電火花沉積 Zr/WC 復合涂層可以改善其表面性能。
關鍵詞: TA2; Zr; WC; 電火花沉積; 復合涂層; 界面行為
電火花沉積( ESD) 是利用高電流使旋轉的焊材與被焊工件產生動態短路,通過在工件上堆積產生冶金結合點,對工件表面進行強化處理的一種表面工程技術。電極材料與工件金屬接觸放電產生高能量脈沖,電極熔化過渡到工件表面微熔的熔池中,從而形成合金化的表面強化層,改變了工件表面的耐磨性、耐蝕性、疲勞強度等,大大提升了工件的壽命[1]。與其它涂層技術相比,電火花沉積技術具有獨特的優點,例如沉積工藝過程簡單、基本不變形、沉積層結合強度高、修復工件的成本低、熱輸入量低、設備小巧便于攜帶、維修方便等[1],近年來越來越多地應用到航空航天、核工業、軍事、醫療機械等各個領域。鈦的比強度高而密度小,機械性、韌性和抗蝕性能好,在高溫下仍具有較好的力學性能,對人體無任何輻射,因此被廣泛應用于航空航天工業、核能發電、海洋科學、汽車工業和醫學領域。但是鈦的硬度較低、導熱系數小、不易導熱,很容易與對磨材料發生粘著磨損,導致零件的磨損失效[2—3]。為了改善其耐磨性,本文研究 TA2 表面電火花沉積 Zr/WC 復合涂層的微觀特征及性能。
1.試驗
采用 DZ-4000 Ⅱ型電火花堆焊機,輸出電壓為AC 220 V、單相 50 /60 Hz,輸入功率為 4000 W,放電頻率為 1400 Hz。電極夾緊在沉積槍上,處于中心位置繞電極軸線旋轉,電極伸出長度在 20 mm 以內,電極材料為 Zr、WC 電極。沉積基體 TA2 樣尺寸(長、寬、高) 為: 15 mm × 15 mm × 10 mm。先分別用 400#、600#、1000#砂紙打磨試樣,再用丙酮和酒精清洗待沉積表面,然后按表 1 中的工藝進行沉積。
表 1 電火花沉積工藝
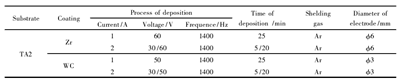
用日本 JSM-560LV 型掃描電鏡觀察涂層形貌; 用美國 EDX 型能譜分析儀分析復合涂層元素; 用日本理學 MSF-3M 新型 X 射線應力分析儀檢測分析復合涂層的殘余應力; 用 HV-1000 型顯微硬度計檢測涂層、過渡層、基體的顯微硬度,加載 200 g,15 s; 在 MH-600 型摩擦磨損試驗機上進行室溫干摩擦磨損試驗,對磨試樣為直徑 6 mm 的 YG8 硬質合金球,轉速為1200 r / min,載荷為 10 N,時間為 30 min,再用精確到0. 1 mg 的 AEL-200 型電子分析天平稱量試樣。
2.結果分析
2.1 涂層形貌分析
2.1.1 表面形貌
圖 1 為涂層的表面 SEM 形貌。涂層表面有很多凹坑( A 點) ,是由沉積脈沖產生的強放電力使合金化的熔滴飛濺形成,電火花沉積時產生很大的放電力,使加工表面產生凹坑輪廓。同時在涂層表面還存在粘連現象( B 點) ,這是由于在火花放電過程中電極和基體材料同時熔化,熔化的電極材料向基體過渡,熔化的基體材料也向電極過渡,在電極與基體不斷分離與接觸的過程中兩者熔為一體,隨著放電次數的增加,粘連的形貌遍布涂層的表面。強化時間較短時,熱輸入量低,電極與基體粘連現象不明顯,粘連層比較薄; 隨著強化時間增加,熱輸入量的增加,粘連現象變得嚴重,會形成具有一定厚度的粘連層[4—5]。
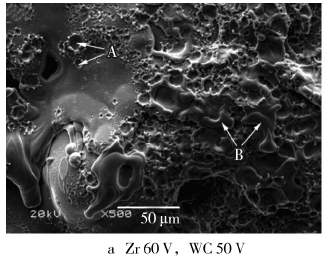
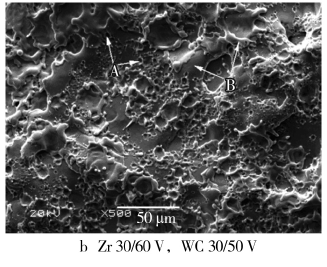
圖 1 涂層表面形貌
2.1.2 斷面形貌
圖 2 為涂層的斷面 SEM 形貌。涂層厚度約 50 ~80 μm。涂層與基體相互熔合,二者之間存在一個熔滲擴散區,有利于提高涂層與基體的結合強度。涂層內有氣孔( A 點) 與裂紋( B 點) 。產生氣孔的原因可能是受電極和基體表面不潔凈和周圍環境的影響,氣孔使強化層變得疏松。產生裂紋的原因,一方面是受電極材料和基體材料成分以及強化環境的影響,使強化層中存在夾雜物和氣孔,降低了強化層的機械強度; 另一方面是由于沉積過程中產生的熱應力導致,沉積過程中熔化的金屬材料遇冷急劇冷卻而凝固,沉積層內存在著熱應力作用,在無數次放電作用下,沉積層反復受到熱沖擊,最終產生顯微裂紋[6—7]。
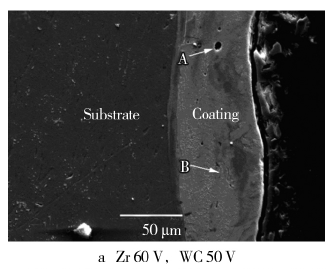
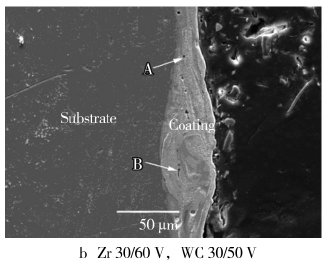
圖 2 涂層斷面形貌
2.2 元素分析
圖 3 為涂層的元素分布,可以看出,涂層與基體結合面處有一個很窄的成分熔滲擴散區,基體與涂層之間發生了元素的相互擴散,基體中的 Ti 由基體向涂層擴散,涂層中的 Zr、W、C 由涂層向基體擴散。但由于沉積過程中高溫時間短,元素擴散不充分。C 和Zr 的含量在沉積層和靠近沉積層的基體中含量較均勻,說明 C 和 Zr 容易擴散。Ti 元素在基體中含量較多,由基體到涂層 Ti 元素含量呈下降趨勢[8—9]。從基體到涂層,W 元素含量逐漸增加,而在涂層中某些部位 W 元素含量較多,可能是沉積過程中硬質合金WC 隨著電極的旋轉作用直接進入了涂層內部所致,對于 W 元素在涂層內部部分區域大量聚集的原因有待做進一步的研究。涂層與基體之間發生了元素的擴散,基體 TA2 中的 Ti 元素進入復合涂層內部,電極材料中的 Zr、W 元素也進入涂層內部,說明電火花沉積是電極與基體材料的相互熔滲過程[10]。
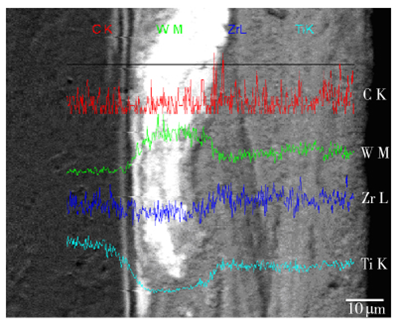
圖 3 涂層到基體元素分布
2. 3 試樣殘余應力分析
由表 2 可知,電火花沉積后的試樣表面有較大的殘余應力,這種殘余應力的產生是一個非常復雜的過程,主要有兩方面的原因: 一方面,在電火花沉積過程中,熔化的工件材料在空氣中遇冷而凝固,工件表面溫度分布不均勻,存在溫度梯度,形成了熱應力,熱應力的存在使涂層表面有產生殘余拉應力的趨勢; 另一方面,在工件材料急熱、急冷過程中,工件材料的組織發生相變會產生相變應力,這會松弛電火花沉積過程中產生的殘余拉應力,并可能向壓應力產生逆轉[11]。
電火花沉積是一個多次重復的過程,對于某一個加工點來說,它的應力情況是多次放電作用的最終結果,這取決于哪個影響因素占主導地位[12]。若熱應力占主導地位,則產生殘余拉應力,若相變應力占主導地位,則產生殘余壓應力。而通過改變電火花沉積規范可以控制殘余應力的性質,如試樣 1 表現為殘余拉應力,試樣 2 表現為殘余壓應力。
表 2 涂層殘余應力
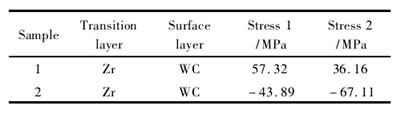
2.4 涂層的耐磨性能
圖 4 是同一個涂層斷面處不同位置的 3 條顯微硬度分布曲線。可以看出,3 條線走勢大致相同,涂層表面的顯微硬度值遠高于基體材料 TA2,最高處可達 965HV200 g; 隨著與涂層表面距離的增加,即由涂層到過渡層,顯微硬度值逐漸下降,而基體的顯微硬度約為 220HV200 g; 涂層表面的顯微硬度約是基體的 4 倍。沉積層之所以有這么高的顯微硬度主要是由于經過電火花沉積后表層組織得到了細化,又引入了較高的殘余壓應力,同時由于沉積層具有高硬度的碳化物 W2C 所致[13]。

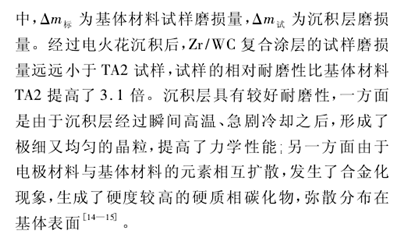
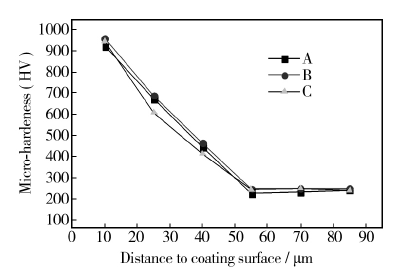
圖 4 距涂層表面的顯微硬度分布曲線
表 3 磨損失重結果
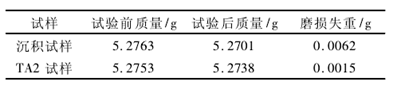
3.結論
1) 利用電火花沉積技術,分別以 Zr、WC 棒為電極,在 TA2 基體表面電火花沉積制備出了連續、均勻的 Zr/WC 復合涂層,復合涂層厚度約為 50 ~ 80 μm,涂層表面較平整,存在較多凹坑和粘連,涂層斷面有少量氣孔和裂紋。
2) Zr / WC 復合涂層與基體間各主要元素發生了相互擴散,涂層中的 Zr、W 主要向基體擴散,基體中的 Ti 元素向復合涂層擴散,過渡層中存在 Zr、W 與 Ti的相互擴散,部分區域硬質合金 WC 大量進入涂層內部。
3) 電火花沉積表面的殘余應力隨加工工藝的不同,可能產生殘余拉應力或殘余壓應力,改變工藝參數可控制殘余應力。4) Zr / WC 復合涂層的表面顯微硬度值最高達965HV200 g,約為基體的 4 倍,沉積層的相對耐磨性比基體增加 3.1 倍,基體表面性能已經發生改變。
投稿箱:
如果您有機床行業、企業相關新聞稿件發表,或進行資訊合作,歡迎聯系本網編輯部, 郵箱:skjcsc@vip.sina.com
如果您有機床行業、企業相關新聞稿件發表,或進行資訊合作,歡迎聯系本網編輯部, 郵箱:skjcsc@vip.sina.com
更多相關信息